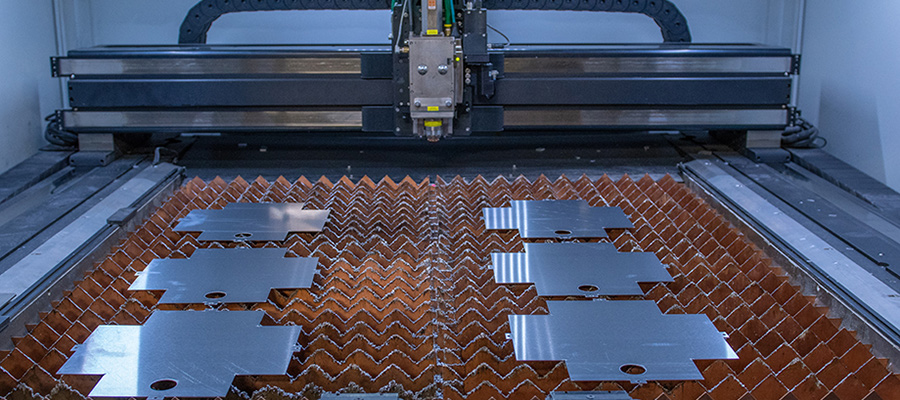
In the field of metal processing, laser cutting is a critical tool for sheet metal cutting. There are several sheet metal forming procedures that may be performed using laser cutting. Sheet metal goods may be made with this machine. When it comes to cutting sheet metal, the laser cutting machine is more adaptable than a traditional cutting machine. Discover how laser cutting in sheet metal processing may be used by continuing to read this article.
Laser cutting is a quick and effective way to cut metal because it makes use of a powerful laser beam. These devices, also known as laser direct cutting machines, are utilised in a variety of production sectors including beverage cans and sheets, packaging materials, and solar panels.
The laser cutting machine is used to cut through the items in a few simple steps:
1. Preparation of the Material
Laser cutting begins with the preparation of the material to be cut. A number of processes may be used based on the sort of product that is to be manufactured.
2. Marking the material after it has been measured
Once the material has been generated, the laser cutter has to know where to cut it. The use of a template or stencil ensures the correctness of this process.
3. Laser cutting machine positioning of the material.
Following this, the laser cutter must be used to locate the item to be sliced. In order to cut the material, it must be firmly in place and positioned properly.
4. Focusing the laser beam on the material’s designated region
The laser beam must be focused on the defined region of the material before cutting can commence. As a result, just that particular region will be harmed throughout the cutting procedure.
5. Cutting the substance using a laser beam that has been activated.
Laser cutting is a fast and accurate method of removing metal from a piece of metal. A high-powered laser beam is used by a laser cutting equipment to precisely cut through the material in a designated region. Laser cutting is regarded to be one of the most effective methods for processing sheet metal because of its quick lead time. Because it doesn’t need a lot of physical work, it is great for organisations who need to swiftly ramp up production.
Various Forms of Sheet Metal
Generally speaking, sheet metal has a thickness of no more than 6 millimetres. Some of the metals that can be used to make it are aluminium, brass, copper, steel, tin, and titanium. Sheet metal is used in a lot of different ways, from making cars to building houses.
Cold-rolled sheet metal and hot-rolled sheet metal are the two most common forms of sheet metal. Hot-rolled sheet metal is steel that has been heated to very high temperatures and then rolled into sheets. By running steel through cold-rolling rollers at lower temperatures, it can be made harder and less flexible. This makes cold-rolled sheet metal a more durable choice.
Products that need a lot of shape and forming, such as automobile body panels and building materials, often employ hot-rolled sheetmetal. Roofing and bracing materials, for example, often employ cold-rolled sheet metal because of its strength and rigidity.